Новости
Нефтегазовая пром.
02.04.2025
Выставки
Наука и технология
02.04.2025
02.04.2025
Теги
Андрей Никипелов: готовим проект атомной станции для производства водорода.
27.12.2021
Нефтегазовая промышленность
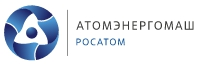
- Андрей Владимирович, что особого, значимого в уходящем году машиностроители "Росатома" положили в свою "копилку"?
- В плане бизнеса уходящий 2021 год был для нас в целом успешным. По результатам года мы снова ожидаем рост выручки и портфеля заказов. Эти показатели дивизиона последние годы непрерывно растут, и даже пандемии не удалось изменить этот позитивный тренд.
"Атомэнергомаш" является ключевым поставщиком оборудования для всех проектов "Росатома" по строительству АЭС. Сейчас в производстве на наших предприятиях находится оборудование для восьми атомных энергоблоков, подавляющее большинство из которых - зарубежные.
В России для Курской АЭС-2 дивизион поставляет реакторную установку нового типа - ВВЭР-ТОИ (водо-водяной энергетический реактор типовой оптимизированный и информатизированный). Изготовление первого комплекта оборудования (реактора и четырех парогенераторов) уже завершено, сейчас делаем второй. В корпусе этого реактора уменьшено количество сварных соединений с шести до четырех - исключены сварные соединения в активной зоне. Это снижает радиационное воздействие на швы и улучшает эксплуатационные характеристики корпуса, что позволит после 60 лет эксплуатации продлить срок его службы еще на 40 лет, то есть жизненный цикл наших реакторов может составить целый век!
- Сейчас все больше на слуху разработки и планы "Росатома" по малым энергоблокам на основе реакторов, уже опробованных на практике в проектах наших атомных ледоколов. Чем здесь пополняется портфель "Атомэнергомаша"?
- Что касается транспортных реакторов РИТМ-200, то мы продолжаем работу над установками для двух универсальных атомных ледоколов - "Якутия" и "Чукотка". Летом следующего года планируем отгрузить два реактора для "Якутии" (третий серийный ледокол проекта 22220), в конце 2023-го - еще два реактора уже для "Чукотки" (четвертый серийный ледокол).
Уходящий год был для АЭМ важным с точки зрения расширения бизнеса. Мы подписали договор на поставку четырех модернизированных плавэнергоблоков для Баимского горно-обогатительного комбината на базе восьми РИТМов. Это первый в мире проект электрификации коммерческого предприятия с использованием плавучих атомных электростанций - совершенно беспрецедентное для "Росатома" и для мировой энергетики событие, в том числе в области применения "зеленой генерации".
Для "Росатома" плавучие энергоблоки - крайне перспективный продукт и для внутреннего, и для внешнего рынков. А для "Атомэнергомаша" - это еще и большой продукт, за который мы отвечаем, что называется, от начала до конца. Если в проектах для ледоколов мы находимся в статусе поставщика оборудования, то в отношении плавэнергоблоков АЭМ - уже поставщик всего "конечного" продукта. Для нас это непростая задачка в том числе и из-за крайне сжатых сроков поставки: ввод первых двух энергоблоков в эксплуатацию в районе мыса Наглёйнын ожидается к началу 2027 года, третьего - к началу 2028 года, четвертого - к началу 2031 года.
В этом году "Атомэнергомаш" успешно завершил строительство уникального стенда для испытаний критического оборудования для производства СПГ. Комплекс расположен в Петербурге на площадке НИИЭФА имени Ефремова. Он рассчитан на три большие номенклатуры: насосы, детандеры и компрессоры. АЭМ, в первую очередь, заинтересован в испытаниях насосов, поскольку мы сами их производим. Первые испытания нашего оборудования уже идут.
- Что касается плавучих энергоблоков для Баимского ГОКа, было объявлено, что их корпуса будут делать в Китае, а реакторные установки - в России. Насколько такая ситуация будет трудна с точки зрения синхронизации работ?
- Не только реакторы будут производиться в России, но и все остальное - турбины, системы управления и все работы по их монтажу будут проведены здесь. За рубежом будут изготовлены только два корпуса. Мы и эти корпуса тоже заказали бы в России, если бы позволяли производственные возможности отечественных верфей.
Вопрос синхронизации работ действительно непростой, особенно с учетом того, что технический проект МПЭБ постоянно корректируется. Для того, чтобы немного облегчить себе задачу, мы с самого начала - еще при подготовке к конкурсу по выбору зарубежного поставщика - определили, что российский судостроитель будет участвовать в приемке этапов работ на зарубежной верфи и подтверждать соответствие этих этапов документации и технологии достройки.
Естественно, в процессе доработки технического проекта, а потом и разработки рабочей конструкторской документации, могут быть изменения, которые потенциально приведут к каким-то несостыковкам при достройке, но это все решаемо. Перед нами стоит задача поставить заказчику продукт в заданные сроки, поэтому сделаем все, чтобы эту задачу выполнить.
- В 2021 году была анонсирована и разработка "Атомэнергомашем" плавучего атомного энергоблока на базе реакторной установки РИТМ-400 для якутского СПГ-проекта "Глобалтэка". В каком состоянии сейчас находится техническое проектирование нового энергоблока? Кто еще может быть заказчиком таких мощных "плавучек"?
Сейчас мы в начале разработки технического проекта такого плавэнергоблока. Подписание контракта на поставку МПЭБ для Баимского ГОКа, а также мировой тренд на декарбонизацию подогревают интерес к атомным плавучим энергоблокам. Ведем обсуждение по этой теме.
- Можете ли вы назвать предварительные финансовые показатели, с которыми "Атомэнергомаш" завершает год?
- Как я уже сказал, выручка и портфель наших заказов на протяжении последних лет постоянно растут. С 2016 года наш портфель вырос более чем в два раза. Выручка - почти вдвое. В 2021 году выручка АЭМ увеличилась более чем на треть по отношению к предыдущему 2020 году. Несмотря на уже имеющийся огромный портфель заказов, продолжаем прирастать и по этому показателю тоже.
Расти такими гигантскими темпами очень сложно. Получать новые контракты с такой же скоростью тоже будет непросто. Если до этого у АЭМ темпы прироста портфеля сильно превышали темпы прироста выручки, то сейчас наоборот: темпы прироста выручки будут сильно превышать темпы прироста портфеля. Но это нормальный процесс.
Наша задача на ближайшие годы - обеспечить выполнение дорожной карты в сочетании с выполнением целей по новым продуктам и рынкам - по плавэнергоблокам, газонефтехимии, мусоросжиганию - по всем тем направлениям, где мы активно движемся вперед.
- Такой активностью, конечно, можно по праву гордиться. Но как холдингу удается в условиях пандемии выполнять плановые показатели, прежде всего по производству оборудования для АЭС, строящихся с участием "Росатома" за рубежом? И кстати, каков сейчас процент вакцинированных среди сотрудников машиностроительного дивизиона?
- Начну с ответа на последний вопрос: мы очень последовательно занимались вакцинацией, уже вакцинированы 86% сотрудников "Атомэнергомаша". Теперь мы так же последовательно занимаемся ревакцинацией. Когда эпидемия только началась, весной прошлого года наши предприятия простояли меньше недели - практически все они сразу вошли в список стратегических и продолжили работу. При этом, конечно, мы разработали и до сих пор применяем все необходимые протоколы, позволяющие минимизировать распространение болезни среди сотрудников.
Пандемия неизбежно отразилась на производственном процессе. Большую часть оборудования мы делаем для зарубежных проектов - для АЭС в Турции, Бангладеш, Индии, Китае, Финляндии и Венгрии. При этом часть оборудования для одного и того же проекта может производиться в России, часть - в Венгрии или в Чехии. По правилам заказчик должен приехать на закрытие контрольных точек по приему качества изготовления. Поэтому, когда закрылись границы, нам пришлось изобретать способы, как не вылететь из производственного графика. Например, на ряде предприятий мы стали использовать оборудование дополненной реальности. С его помощью мы осуществляли взаимную приемку между нашими площадками (проходили оценку на так называемых точках останова, когда представители заказчика убеждаются, что операция проведена корректно). С помощью такой "дистанционной приемки" для клиента был создан эффект присутствия без приезда на предприятие. Находясь перед экраном компьютера, заказчик может осмотреть изделие глазами "аватара", по связи задать интересующие вопросы, изучить результат в подробностях.
- Предлагаю теперь поговорить как раз о цифровых технологиях. Они все больше становятся необходимой составляющей в разных отраслях промышленности, и, конечно, в атомной. Каким образом они внедряются на предприятиях "Атомэнергомаша"?
- "Цифра" - это вообще отдельная большая тема для разговора. Но если в двух словах, то мы занимаемся цифровизацией на предприятиях всего дивизиона, цифровые процессы внедряются по всем направлениям: от комплексного планирования производства до контроля режима эксплуатации ключевых станков и оборудования. Для заказчиков создаем цифровые паспорта изделий, которые позволяют контролировать наше оборудование на всех этапах его жизненного цикла.
Сейчас мы работаем над тем, чтобы у всех подразделений и предприятий АЭМ появилось общее пространство для обмена данными. Создаем электронные двойники нашей продукции и процессов ее производства, то есть, грубо говоря, оцифровываем не только данные об изделиях, но и весь жизненный цикл продукции: начиная от конструкторской разработки, планирования и закупки материалов и заканчивая производством и транспортировкой оборудования.
Например, одна из актуальных задач - создание единой системы производственного планирования в масштабе дивизиона с учетом перспективы загрузки на годы. При этом она напрямую интегрируется с системами планирования предприятий. Мы собираемся обеспечить долгосрочное планирование на весь объем отраслевого заказа, а также на среднесрочный (до года) и краткосрочный (до месяца) горизонты.
К задаче планирования производства, которая определяет "такт" работы предприятия, мы подстраиваем цифровизацию поддерживающих процессов. Например, закупочные службы, получая задания из производственного плана, должны обеспечить бесперебойное снабжение, конструкторы и технологи - выдавать вовремя затребованную проектную и рабочую документацию.
- Андрей Владимирович, российская атомная отрасль всегда имела и сейчас обладает великолепной научной базой. Свои исследовательские центры есть, разумеется, и у "Атомэнергомаша". А какие их основные результаты за последнее время вы бы отметили?
- Как вы понимаете, продукция дивизиона - большое или очень большое "железо", поэтому для нас материаловедение, сварочные технологии, спецстали и спецпокрытия - это "наше все". От них напрямую зависит качество нашего оборудования и прогнозирование его ресурса.
Наши ученые-материаловеды в Центральном научно-исследовательском институте машиностроения впервые в России разработали технологию и создали оборудование для подводной полуавтоматической сварки. Эту технологию можно использовать в судостроении, при проведении сварочных работ на глубине, при прокладке подводных трубопроводов, выполнении различных ремонтных работ на объектах портовой инфраструктуры и в других сферах.
Продолжаем разрабатывать оборудование для СПГ-проектов, например, насосы для перекачки сжиженного газа. С этим оборудованием мы активно пытаемся выйти на новые рынки - из-за монополии зарубежных производителей даже на нашем внутреннем рынке это сложная задача. Нам нужно доказать, что наши насосы точно не хуже зарубежных. И здесь без материаловедения тоже не обойтись: среду, в которой работают СПГ-насосы, "приветливой" не назовешь (температура сжиженного СПГ - ниже минус 160 градусов).
Для понимания: это температуры, не очень сильно далекие от абсолютного нуля (минус 273), а абсолютный нуль - это температура, при которой останавливается любое движение частиц. На практике такая температура не достижима. Чтобы наше оборудование успешно работало при подобных сверхнизких температурах, научные подразделения АЭМ совершенствуют сплавы, из которых оно делается. ЦНИИТМАШ разработал технологию промышленного производства толстолистового проката из трех криогенных марок стали. По своим характеристикам новые марки стали превосходят существующие аналоги российского и зарубежного производства и при этом позволяют на четверть снизить затраты при изготовлении оборудования для СПГ.
Если дальше говорить о перспективных проектах, то мы готовы перейти к активной фазе строительства коммерческого реактора на быстрых нейтронах - БН-1200М. Наше предприятие "ОКБМ Африкантов" завершает разработку технического проекта. Чтобы сделать блок более конкурентоспособным, была проведена большая работа: реакторная установка стала меньше, компактнее и мощней. Наши конструкторы смогли уменьшить здание реакторного отделения, а мощность реактора - увеличить. Капиталоемкость всего реакторного отделения для будущей станции уменьшилась в целом на 30%. По отдельным направлениям БН-1200М у нас еще будут продолжаться работы, связанные с НИОКР, но, в целом, мы готовы и ждем решения на уровне государства, чтобы приступить к выполнению задачи по строительству такого энергоблока.
"Атомэнергомаш" участвует также в проекте по созданию опытно-демонстрационного реактора на быстрых нейтронах с жидкометаллическим свинцовым теплоносителем "БРЕСТ-ОД-300" - первого в мире энергоблока четвертого поколения с быстрым реактором естественной безопасности. В июне 2021 года на площадке "Сибирского химического комбината" в Северске стартовало его строительство. Наш завод "ЗиО-Подольск" поставляет для БРЕСТа восемь парогенераторов. А наше Центральное конструкторское бюро машиностроения (ЦКБМ) разрабатывает главные циркуляционные насосные агрегаты (ГЦНА) первого контура.
- Прямо скажем, нетривиальная вещь для атомной энергетики.
- Да, разработка ГЦНА для реактора БРЕСТ-ОД - непростая задача, поскольку в реакторе мощностью 300 МВт в качестве теплоносителя применяется не вода, как в ВВЭРах, а расплав свинца с номинальной температурой 420 градусов Цельсия. В ближайшие два года в рамках нового этапа опытно-конструкторских работ планируется изготовить опытный образец ГЦНА-1720. После проведения комплекса испытаний и корректировки конструкторской документации будут запущены в производство четыре насосных агрегата.
Постепенно движемся и в развитии аддитивных технологий. Так, в этом году впервые в России на 3D-принтере ЦНИИТМАШа была изготовлена деталь энергоустановки для атомного ледокола (так называемого сепарационного модуля). Также ее можно применять в оптимизированных плавэнергоблоках. Применение аддитивных технологий для серийного изготовления этой детали позволит сократить время производства в среднем до четырех раз.
- На волгодонском "Атоммаше" уже изготовлен корпус многоцелевого исследовательского ядерного реактора на быстрых нейтронах МБИР. Он, как известно, должен помочь обеспечить России мировое лидерство по части экспериментальной базы атомной энергетики будущего. Вообще, насколько сложной была работа атоммашевцев (все-таки это штучный продукт), какие новые компетенции потребовались? Какова сейчас судьба изделия?
- Это действительно штучный продукт. Такие реакторы, как МБИР, строятся раз в 50 лет: предыдущий реактор БОР-60 был запущен в эксплуатацию в 1968 году. За это время происходит колоссальный разрыв между изначальной идеей, технологиями и существующей производственной цепочкой. Наиболее сложным моментом в процессе изготовления корпуса МБИР является работа с тонколистовыми элементами из нержавеющей стали с очень жесткими требованиями по точности. Часть размеров необходимо было получать после сварочных операций без возможности исправления механической обработкой. И "Атоммаш" с такими задачами успешно справился. Сейчас корпус реактора находится на завершающей операции - идет контрольная сборка. В ходе этой операции окончательно проверяется достижение проектных геометрических параметров всех элементов и подтверждается работоспособность реактора.
- Большим направлением в российской энергетике в последнее время стала водородная энергетика, и "Росатом" активно включился в ее развитие. В какой мере здесь задействован "Атомэнергомаш"?
- Участие "Атомэнергомаша" в водородных проектах рассматривается по нескольким направлениям: это и разработка проекта атомной энерготехнологической станции (АЭТС) для производства водорода, и создание систем оборудования для его хранения и транспортировки.
Сейчас ОКБМ завершает разработку эскизного проекта реакторной установки ВТГР (высокотемпературный газоохлаждаемый реактор). Согласно дорожной карте, в 2023 году должен быть завершен техпроект реакторной установки ВТГР атомной энерготехнологической станции (АЭТС). В начале 2025 года мы должны получить лицензию на размещение АЭТС, а к осени этого же года разработать проектную документацию. Физический пуск первого блока АЭТС намечен на конец 2032 года, а в декабре 2035 года ожидается введение головной АЭТС в промышленную эксплуатацию.
Корпус реактора ВТГР возможно изготовить, например, на нашем "Атоммаше" - по технологии изготовления корпуса для ВВЭР-1000.
- А в производстве какого именно неядерного оборудования для водородной энергетики заинтересован "Атомэнергомаш"?
- АЭМ заинтересован в расширении своего бизнеса в принципе. Что касается водородной темы, наши компетенции позволяют нам освоить изготовление систем оборудования для всех технологических переделов: производство, транспортировка и применение водорода. Например, речь может идти об изготовлении установок парогазовой конверсии метана, улавливания углекислого газа, системы хранения и транспортировки водорода, оборудования для водородной заправочной инфраструктуры.
- Тема строительства мусоросжигательных заводов сейчас получает новое наполнение в контексте зеленого энергоперехода. Эксперты полагают, что современные технологии переработки мусора в энергию вполне могут служить целям декарбонизации. Предприятие "Атомэнергомаша" "ЗиО-Подольск" уже выступает производителем и комплектным поставщиком котлового оборудования для мусоросжигательных заводов, строящихся компанией "РТ-Инвест" в России по технологии Hitachi Zosen Inova. Просматриваются ли новые совместные проекты по переработке отходов как в России, так и за рубежом?
- Что касается декарбонизации, для того чтобы снижение выбросов СО2 стало ощутимым, таких заводов по переработке отходов в энергию должно быть много, пара-тройка МСЗ на снижение выбросов СО2 вряд ли повлияет. Озвученной целью строительства этих заводов является борьба со свалками. МСЗ, которые строятся в Московской области, позволят снизить уровень захоронения отходов в регионе на треть. Пока строятся четыре завода под Москвой и один в Казани. Мы ожидаем решения по строительству МСЗ в других регионах. "Атомэнергомаш" заинтересован в участии в таких проектах - у нас уже наработаны все необходимые уникальные компетенции, есть нужные производственные мощности и высококвалифицированные кадры.
АЭМ в работе над проектом для мусоросжигания было важно несколько моментов: это возможность освоения новых уникальных технологий и возможность получить опыт и референции для развития этого бизнес-направления дальше, причем не только в России. Референцию за рубежом мы уже получили: в 2020 году "Атомэнергомаш" принял участие в изготовлении и поставках оборудования для завода по энергетической утилизации ТКО "Riverside" в Великобритании. Сейчас мы рассматриваем участие в аналогичных проектах на территории Венгрии, ЮАР, Танзании, Сенегала, Намибии.
- Интересная новость пришла весной нынешнего года - о том, что "Атомэнергомаш" открыл в Архангельске свой филиал, компанию "АЭМ-Пропульсия", которая будет производить и поставлять элементы пропульсивного комплекса для разных судов. Все-таки, в чем был интерес для "Атомэнергомаша" создавать такое собственное направление? Как уже продвигается проект?
- Развитие новых неатомных продуктов - это часть нашей стратегии. Поэтому мы активно ищем новые рынки и выявили весьма интересную нишу на рынке поставок оборудования для судостроения - комплектные поставки составных элементов пропульсивных комплексов, таких как валолиния в сборе, винты и прочее, со всей вспомогательной комплектацией. Пропульсивный комплекс - это настоящий хай-тек в судостроении.
Под реализацию проекта мы задействуем не только существующие мощности предприятий дивизиона, но и организуем собственную площадку в Архангельске, на которой с этим оборудованием будет производиться целый ряд технологических операций. Собираемся инвестировать в это новое для нас направление значительные средства, а пока выбираем подрядчика, который будет производить работы по модернизации выбранного нами производственного комплекса.
- Вернемся к теме испытания СПГ-оборудования на первом российском стенде, построенном при участии "Атомэнергомаша". "Росатому" есть за что испытывать гордость и тут - ведь выполнен крупный, и, без преувеличения, стратегически важный импортозамещающий проект. Но есть ли у вас уверенность в том, что этот объект окажется сполна востребован заказчиками и не будет простаивать?
- Испытания на стенде уже начались - тестируем произведенный "ОКБМ Африкантов" насос отгрузки сжиженного природного газа ЭНК 2000/241 с номинальной подачей две тысячи кубометров в час. На сегодняшний день это самый высокопроизводительный насос из разработанной нашими конструкторами линейки оборудования для производства СПГ. После прохождения тестов он будет использоваться на СПГ-заводе на Ямале.
"Атомэнергомаш" на сегодня - единственный в России производитель насосов для СПГ-проектов, и мы крайне заинтересованы в том, чтобы наше оборудование успешно работало на объектах заказчиков. Испытания на стенде в Петербурге дадут и АЭМ, и нашим клиентам уверенность в надежности и работоспособности наших изделий: как режимы, так и безопасность их работы - теперь все можно проверять в одном месте. Успешные испытания также снимут барьеры и сомнения в возможностях АЭМ по созданию новых высокотехнологичных продуктов.
Что касается востребованности стенда, с самого начала "Росатом" гарантировал равные права доступа к испытаниям всем участникам рынка, поэтому мы рассчитываем на то, что стенд будет востребован, причем не только российскими, но и зарубежными производителями. Российский испытательный комплекс уникален. Здесь установлена самая большая в мире система хранения как криогенных жидкостей в виде жидкого азота, так и СПГ. Есть только две аналогичных площадки, где проводится тестирование СПГ-оборудования, и обе находятся в Америке. Они меньшего размера и принадлежат исключительно компаниям, которые подобное оборудование производят, то есть их испытательные мощности недоступны для "общего использования". Российский же стенд открыт для любых производителей - как отечественных, так и зарубежных. Так что добро пожаловать!
Похожие новости:
17:1224.12.2021
Нефтегазовая промышленность
13:0205.02.2021
Нефтегазовая промышленность
19:0528.05.2019
Нефтегазовая промышленность
13:0204.02.2021
Нефтегазовая промышленность
18:1214.12.2020
Нефтегазовая промышленность